Évolution de l'entretien industriel de l'origine
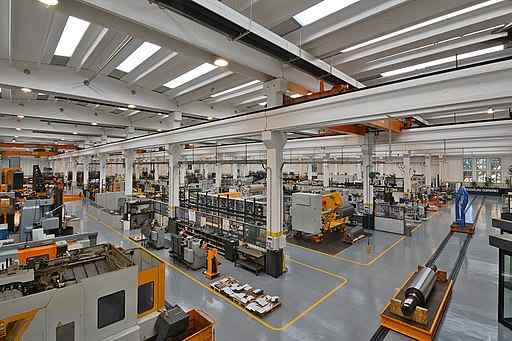
- 1251
- 364
- Prof Ines Gaillard
La Évolution de la maintenance industrielle Il a commencé à être plus significatif après la première de la guerre mondiale, étape dans laquelle les machines devaient fonctionner à une capacité maximale et sans interruptions. Auparavant, le travail était celui qui a effectué près de 90% des travaux, par rapport aux 10% estimés, ils ont fait les premières machines.
La maintenance industrielle provient en même temps que les machines ont commencé à être mises en œuvre pour la production de biens et de services, au début du 19e siècle. En tant que caractéristique commune à toutes ses phases de développement, la nécessité de la rendre de plus en plus spécialisée est présentée.
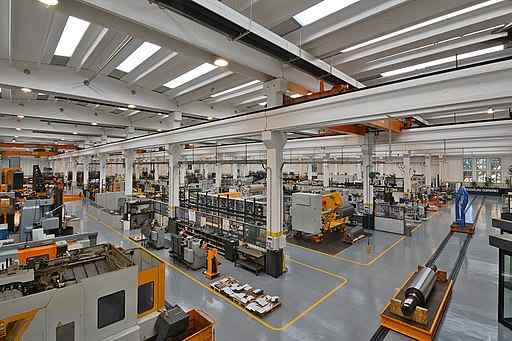
La maintenance industrielle est cet ensemble de mesures techniques organisationnelles, qui peuvent être élaborées auparavant, qui vise à maintenir la fonctionnalité de l'équipement et à garantir un état optimal des machines au fil du temps.
Parmi les objectifs de maintenance industrielle, on peut mentionner: conserver la capacité de travail des machines, réduire les arrêts imprévus, contribuer à l'augmentation de la productivité, conserver en parfait état les moyens de production avec un coût minimum.
Grâce à des plans d'entretien industriel, il est destiné à votre durée de vie utile.
Les tâches de maintenance industrielle ne sont pas exclusives à l'équipement et aux machines, mais de toute installation fixe ou mobile, services industriels, commerciaux ou spécifiques, c'est-à-dire tout type de bien productif.
[TOC]
Étapes de son origine à la présente
Première génération: de la révolution industrielle jusqu'en 1950
Il correspond à Entretien correctif total, dans lequel une rupture devrait procéder à la réparation respective. Cette phase est généralement identifiée avant 1950 et est la plus longue étape car elle commence par la révolution industrielle. Les coûts de maintenance étaient assez élevés et le temps de chômage pour résoudre les problèmes a été prolongé.
Avec la mise en œuvre de la production en série, après la Première Guerre mondiale, les usines ont commencé à établir un minimum de programmes de production et la nécessité de former un équipement qui se concentre sur le maintien des machines des lignes de production et diminue à la lettre possible le moment de l'arrêt.
Peut vous servir: automatisation industrielleParallèle à la zone de production puis à l'entretien qui était axé sur la réparation des défaillances correctives ou d'urgence. De plus, des tâches de prévention ont été affectées pour éviter les échecs.
La maintenance corrective a été caractérisée par la présentation de coûts de main-d'œuvre élevés et les coûts d'opportunité élevés, car la disponibilité de la rechange devrait être immédiate pour pouvoir répondre à tout dommage qui était enregistré.
Parmi les inconvénients les plus évidents figurent une affectation de qualité en raison de l'usure progressive de l'équipement, du risque de ne pas avoir la disponibilité de remplacement, ce qui signifiait de grands coûts, des temps tués par des échecs soudains et un risque que d'autres problèmes puissent être générés en parallèle.
Deuxième génération: de 1950 à 1970
Les travaux de maintenance préventive étaient déjà systématisés pour l'avènement de la Seconde Guerre mondiale. Et quelques années plus tard, l'American Quality Control Society a émergé, ce qui a aidé à réaliser l'étude statistique du travail, améliorant également la qualité des produits obtenus.
La deuxième génération se concentre sur le maintenance préventive des pannes, de sorte que des œuvres cycliques et répétitives sont réalisées avec une certaine fréquence pour la réalisation dudit objectif. Cette phase s'étend jusqu'à la fin des années 70.
Dans ce document, des substitutions préventives commencent à être effectuées, car la relation entre la durée de vie de l'équipement et leur probabilité de défaillance est découverte.
La maintenance préventive a plusieurs modalités: il peut s'agir d'un processus à effectuer périodiquement, généralement avec un intervalle de temps de 6 à 12 mois. Il peut également être planifié en fonction des fabricants ou des normes établies par l'ingénierie.
Une autre modalité peut avoir l'intention de mettre en œuvre des améliorations du processus et bien qu'elle n'ait pas de fréquence établie, c'est une refonte pour optimiser le processus. Enfin, il y a un entretien autonome, effectué par l'opérateur avec des activités simples ou celle de la routine.
Troisième génération: de 1980 à 1990
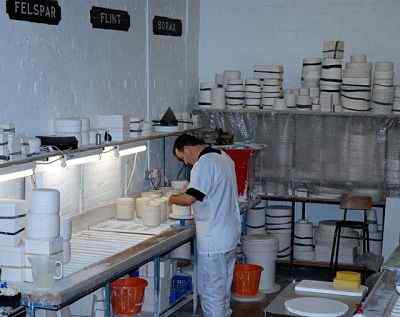
La maintenance est mise en œuvre à condition, c'est-à-dire celle qui dépend de la surveillance des paramètres en fonction du remplacement ou de la reconditionnement des machines.
Peut vous servir: télégraphe: histoire, invention, évolution, comment fonctionneCe travail est rendu possible grâce à la disponibilité d'équipements d'inspection et de contrôle fiables, qui permettent de connaître l'état réel de l'équipement grâce à des mesures périodiques.
C'est le moment de Maintenance prédictive, qui consistait en la détection précoce de symptômes naissants de problèmes futurs. Des études sur les causes sont généralement menées pour découvrir l'origine des échecs. Un élément de différenciation à ce stade est qu'ils commencent à s'impliquer dans les zones de production dans la détection de problèmes.
L'un des grands avantages de la maintenance prédictive est la possibilité de surveillance et d'enregistrement des échecs, il sera donc plus facile de planifier les réparations futures et moins d'interventions de personnel de maintenance seront enregistrées.
Quatrième génération: de 1990 à nos jours
Les débuts de cette phase sont généralement identifiés dans les années 90 lorsque les entreprises américaines avaient déjà intégré à leur dynamique le concept de qualité totale que les industries japonaises avaient promu à partir de 60 ans. La gestion totale de la qualité (TQM) a cherché à créer une sensibilisation à la qualité dans tous les processus de l'organisation et les personnes qui y ont travaillé.
La quatrième génération correspond à Maintenance productive totale qui est inspiré par cette philosophie d'origine japonaise qui cherche l'excellence ou dit dans une phrase: obtenir le maximum avec une qualité acceptable, au moins un coût possible, dans un sens nacré et complet. Pour cela, de petites tâches de maintenance telles que l'ajustement, l'inspection, le remplacement des pièces sont effectuées et l'interaction continue avec le gestionnaire de maintenance.
Le programme s'est concentré sur le facteur humain de l'ensemble de l'entreprise à laquelle les tâches de maintenance préventives sont affectées pour maximiser l'efficacité des marchandises. Il suppose trois principes: gardez toujours les installations en bon état, concentrez-vous sur l'augmentation de la productivité et impliquant la totalité du personnel.
Il s'agit de la phase des systèmes d'amélioration continue et se caractérise par la mise en œuvre d'actions pour l'amélioration et la surveillance des actions. La maintenance devient un avantage, plutôt que comme un mal nécessaire, et est considéré comme un engagement par tous les départements de l'organisation.
L'objectif est d'atteindre l'efficacité totale de l'équipement qui implique l'efficacité économique par la disponibilité, les performances maximales et les produits de qualité.
Il peut vous servir: Système humain-machine: caractéristiques et exemplesDe plus, trois autres outils sont généralement mis en œuvre: l'ingénierie des risques qui implique de déterminer les conséquences des échecs acceptables ou non; l'analyse de fiabilité qui fait référence à l'identification des tâches préventives faisables et rentables; L'amélioration de la maintenabilité qui consiste à réduire les temps et les coûts de maintenance.
À ce stade, il y a eu des changements importants dans la législation sur la sécurité et l'hygiène au travail, ainsi que des pratiques plus amicales à l'environnement. Par conséquent, les dispositifs de purification, les usines d'extraction, l'atténuation du bruit, l'équipement de détection, le contrôle et les alarmes ont commencé à être mis en œuvre.
Aujourd'hui, les experts du domaine estiment que les coûts de maintenance subiront une augmentation progressive qui conduira les industries à générer des produits de maintenance plus fiables et faciles.
Importance de l'entretien
La maintenance industrielle est passée d'un mal nécessaire auquel plusieurs départements d'une organisation sont engagés et impliqués. Cela est essentiellement dû au fait que la véritable importance de la gestion efficace des échecs ou des problèmes d'équipement et d'installations a été reconnue, ce qui peut affecter l'une des étapes de la production de biens ou de services.
Il convient de noter que l'importance de l'entretien industriel réside dans ce qui suit:
- Empêche les accidents de travail et augmente la sécurité des personnes.
- Réduit les pertes dues aux arrêts de production.
- La gravité des échecs qui ne sont pas évités diminue.
- Empêche les dommages qui peuvent être irréparables dans l'équipement ou les installations.
- Garantit les performances acceptables de l'équipement.
- Permet de documenter les processus de maintenance nécessaires pour chaque machine.
- Prolonge la durée de vie utile de l'équipement ou des marchandises.
- Conserve des produits productifs dans des conditions opérationnelles sûres et pré-établies.
- Améliore la qualité de l'activité.
- Permet la préparation appropriée du budget, ajusté aux besoins de l'entreprise.
Les références
- Muñoz Abella, M. (2003) Maintenance industrielle. Madrid: Carlos III Université de Madrid. Zone de génie mécanique.
- Mora Gutiérrez, un. (2009). Entretien: planification, exécution et contrôle. Mexique: éditeur d'Alfaomega Grupo.
- Maintenance industrielle. (s.F.). Récupéré de Ecured.Cu
- Petits enfants. Histoire de l'entretien. (2009, 27 mai). Récupéré de la maintenance industrielle 2009.Blogspot
- Villada, «La maintenance en tant que stratégie concurrentielle», Rev. Facteur. Insigne. Univ. Antioquia, non. 17, pp. 7-13, 1998.
- L'évolution de la maintenance industrielle: blog: ATS. (2019, 26 juillet). Récupéré de AdvancedTech.com
- « Structure de nitrate de sodium (Nano3), propriétés, utilisations, risques
- Concept de distance euclidienne, formule, calcul, exemple »