APQP (Planification avancée de la qualité des produits)
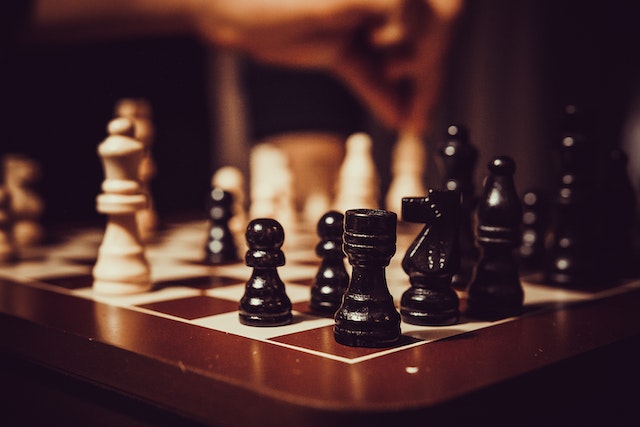
- 3019
- 827
- Eva Henry
Quel est l'APQP?
APQP (Planification avancée de la qualité des produits), En espagnol "Planification avancée de la qualité des produits", est un cadre de procédures et de techniques utilisées pour développer des produits dans l'industrie, en particulier en automobile.
Les produits et chaînes d'approvisionnement complexes ont de nombreuses possibilités d'échec, en particulier lorsque de nouveaux produits sont lancés. APQP est un processus structuré pour la conception de produits et de processus, visant à garantir la satisfaction du client à l'égard de nouveaux produits ou processus.
Cette approche utilise des outils et des méthodes pour réduire les risques associés aux changements dans un nouveau produit ou processus.
Son objectif est de produire un plan standardisé pour les exigences de qualité des produits, ce qui permet aux fournisseurs une conception qui satisfait le client, facilitant la communication et la collaboration entre différentes activités.
Dans le processus APQP, un équipement multifonctionnel est utilisé, ce qui implique la commercialisation, la conception des produits, les achats, la production et la distribution. Ce processus est utilisé par General Motors, Ford, Chrysler et leurs fournisseurs, pour son système de développement de produits.
Phases APQP
APQP sert de guide dans le processus de développement et également comme un moyen standard de partager les résultats entre les fournisseurs et les entreprises automobiles. Il se compose de cinq phases:
Phase 1: planification et définition du programme
Lorsque la demande des clients nécessite l'introduction d'un nouveau produit ou l'examen d'un existant, la planification devient un thème central, avant même les discussions sur la conception ou la refonte du produit.
Dans cette phase, la planification cherche à comprendre les besoins des clients ainsi que les attentes du produit.
Les activités de planification comprennent la collecte des données nécessaires pour définir ce que le client veut, puis utiliser ces informations pour discuter des caractéristiques du produit.
Peut vous servir: secteur primaire: caractéristiques, activités économiques, importanceEnsuite, vous pouvez définir le programme de qualité nécessaire pour créer le produit comme spécifié. Le résultat de ce travail comprend la conception des produits, la fiabilité et les objectifs de qualité.
Phase 2: Conception et développement des produits
Le but de cette phase est de compléter la conception du produit. Voici également une évaluation de la viabilité des produits. Les résultats du travail dans cette phase comprennent:
- Examiner et vérifier la conception terminée.
- Spécifications définies des matériaux et exigences de l'équipement.
- Analyse des effets et mode de défaillance de conception terminée pour évaluer les probabilités de défaut.
- Plans de contrôle établis pour la création du prototype de produit.
Phase 3: Conception et développement du processus de fabrication de produits
Cette phase se concentre sur la planification du processus de fabrication qui produira le produit nouveau ou amélioré.
L'objectif est de concevoir et de développer le processus de production, en tenant compte des spécifications et de la qualité du produit et des coûts de production.
Le processus doit être en mesure de produire les montants nécessaires pour répondre à la demande attendue des consommateurs, tandis que l'efficacité est maintenue. Les résultats de cette phase comprennent:
- Une configuration complète de flux de processus.
- Une analyse d'effet et d'échec du processus complet pour identifier et gérer les risques.
- Spécifications de qualité du processus d'exploitation.
- Exigences d'emballage et de finition des produits.
Phase 4: Validation du processus et du produit
C'est la phase de test pour valider le processus de fabrication et le produit final. Les étapes incluent:
- Confirmation de la capacité et de la fiabilité du processus de production. De même, le critère pour accepter la qualité des produits.
Peut vous servir: intérêt simple: éléments, comment le calculer et exemple- Réalisation des essais de production.
- Test de produit pour confirmer l'efficacité de l'approche de production mise en œuvre.
- Convenir aux ajustements nécessaires avant de passer à la phase suivante.
Phase 5: Lancement, évaluations et amélioration continue
Dans cette phase, le lancement d'une production à grande échelle se produit, mettant l'accent sur l'évaluation et l'amélioration des processus.
Parmi les piliers de cette phase figurent la réduction des variations de processus, l'identification des problèmes et le début des actions correctives pour soutenir l'amélioration continue.
Il existe également la collecte et l'évaluation des commentaires et des données des clients liés à l'efficacité du processus et à la planification de la qualité. Les résultats incluent:
- Un meilleur processus de production, en réduisant les variations de processus.
- Amélioration de la qualité de la livraison des produits et du service client.
- Amélioration de la satisfaction du client.
Exemple
Où incorporer APQP
- Développement des exigences de la voix du client, en utilisant la mise en œuvre de la fonction de qualité.
- Développement d'un plan de qualité de produit intégré dans le calendrier du projet.
- Activités de conception de produits qui communiquent des caractéristiques spéciales ou clés pour traiter l'activité de conception, avant de libérer la conception. Cela comprend de nouvelles formes et pièces, des tolérances plus serrées et de nouveaux matériaux.
- Développement de plans d'essai.
- Utilisation d'une revue de conception formelle pour suivre les progrès.
- Planification, acquisition et installation d'équipements et d'outils appropriés, selon les tolérances de conception données par la source de conception du produit.
Peut vous servir: Institutions économiques: caractéristiques, exemples, objectifs- COMMUNICATION DES SUGGESSIONS par du personnel de l'assemblage et de la fabrication sur les moyens de mieux assembler un produit.
- Établissement de contrôles qualité appropriés pour des caractéristiques spéciales ou des clés d'un produit ou des paramètres d'un processus, qui courent toujours le risque d'échecs potentiels.
- Effectuer des études de stabilité et la capacité des caractéristiques spéciales pour comprendre la variation actuelle et ainsi prédire les performances futures avec le contrôle des processus statistiques et la capacité de processus.
Les industries qui l'utilisent
Ford Motor Company a publié le premier manuel de planification de qualité avancée pour ses fournisseurs au début des années 80. Cela a aidé les fournisseurs à Ford à développer des contrôles adéquats pour la prévention et la détection de nouveaux produits, soutenant ainsi l'effort de qualité de l'entreprise.
À la fin des années 80, les principaux fabricants de l'industrie automobile aux États-Unis ont utilisé des programmes APQ. General Motors, Ford et Chrysler l'ont mis en œuvre et ont ensuite vu la nécessité de se joindre pour créer pour leurs fournisseurs un noyau commun des principes de planification de la qualité des produits.
Les directives ont été établies au début des années 90 pour s'assurer que les protocoles APQP se poursuivent avec un format standardisé.
Les représentants des trois constructeurs automobiles et de l'American Society for Quality Control ont créé un groupe d'exigences de qualité, pour avoir une compréhension commune des problèmes d'intérêt mutuel dans l'industrie automobile.
Cette méthodologie est désormais également utilisée par des entreprises progressistes pour garantir la qualité et les performances grâce à la planification.
Les références
- Planification avancée de la qualité des produits. Pris des solutions NPD.com.
- Planification avancée de la qualité des produits (APQP). Tiré de la qualité -ne.com.